Surface Coating Powders for Industrial Excellence
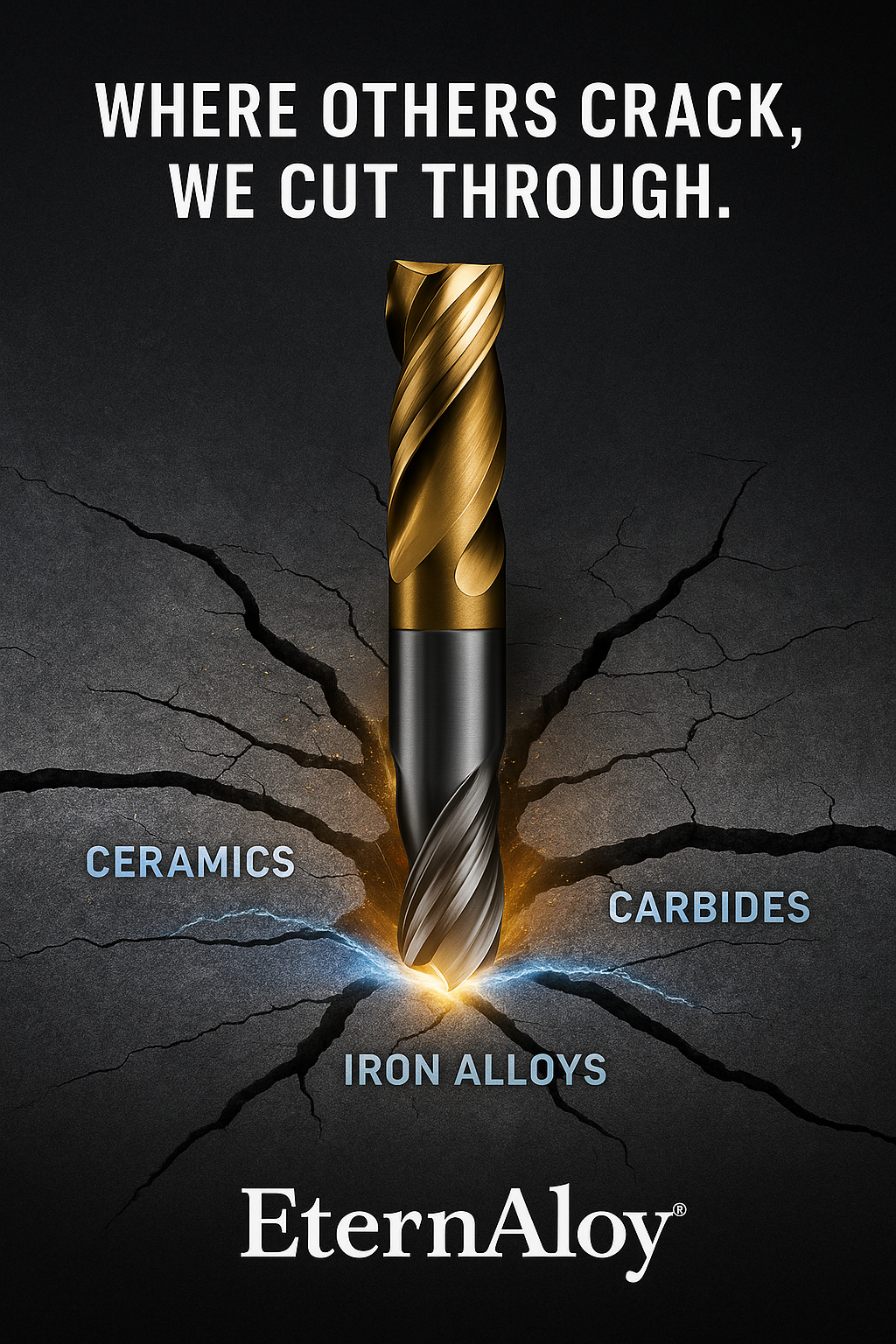
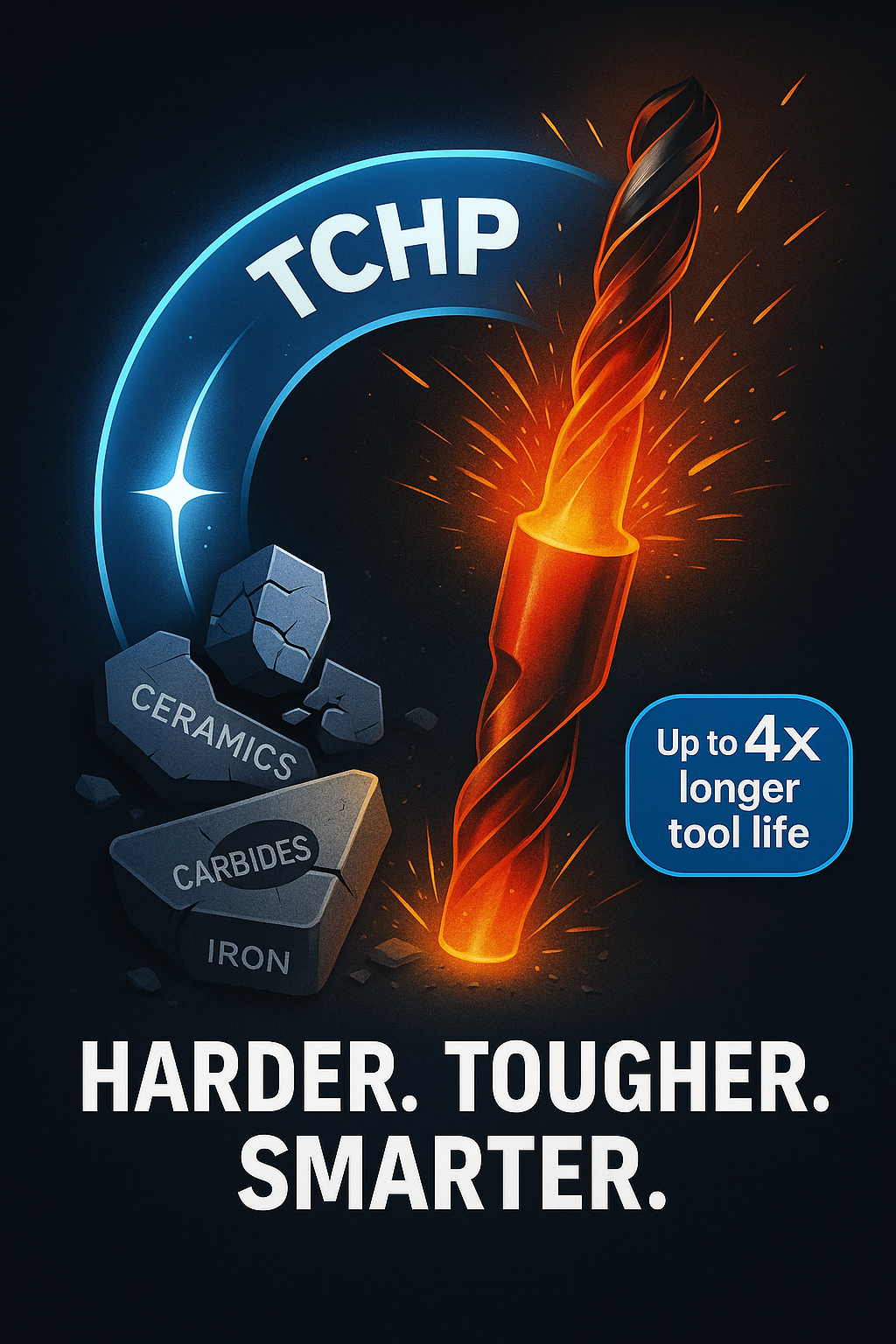
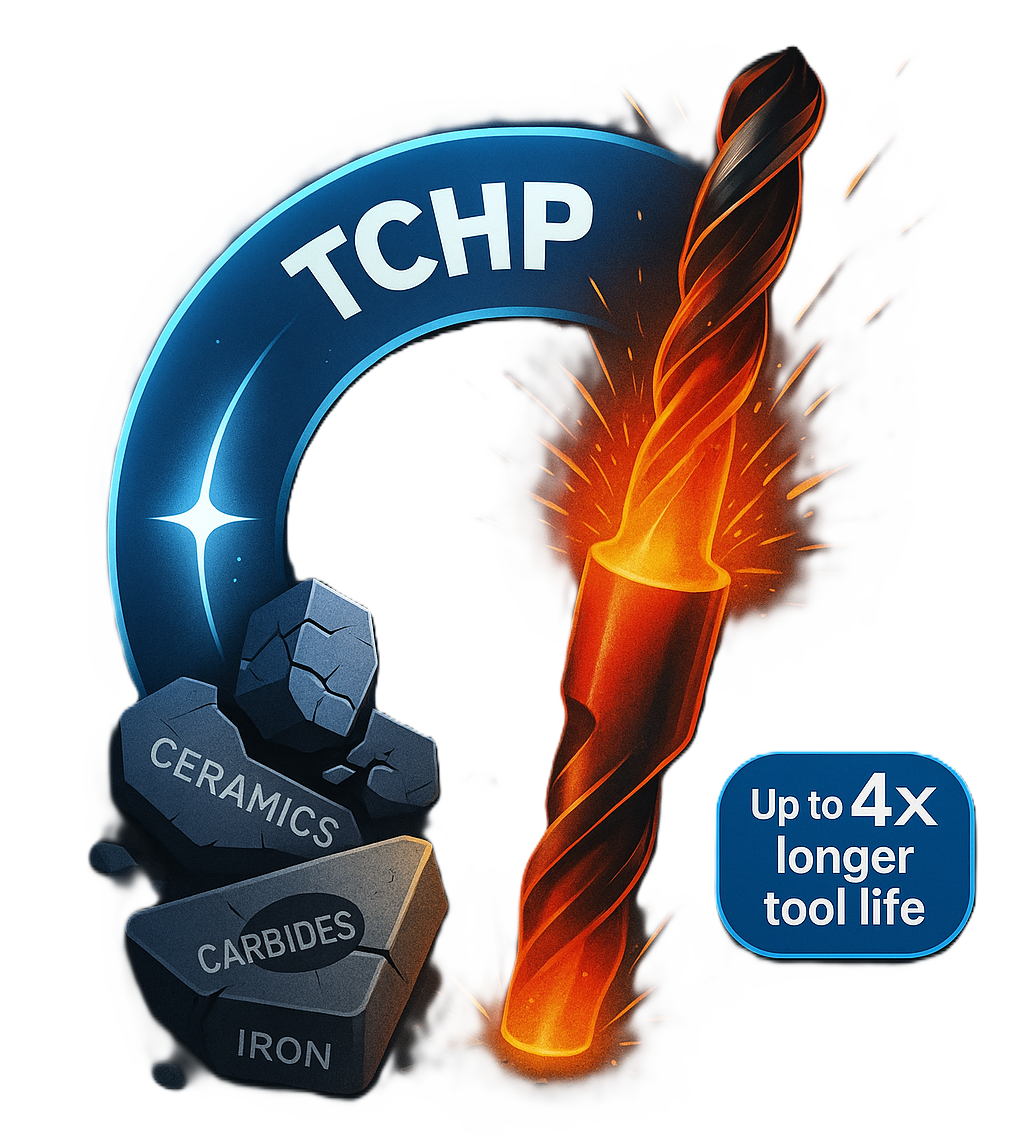
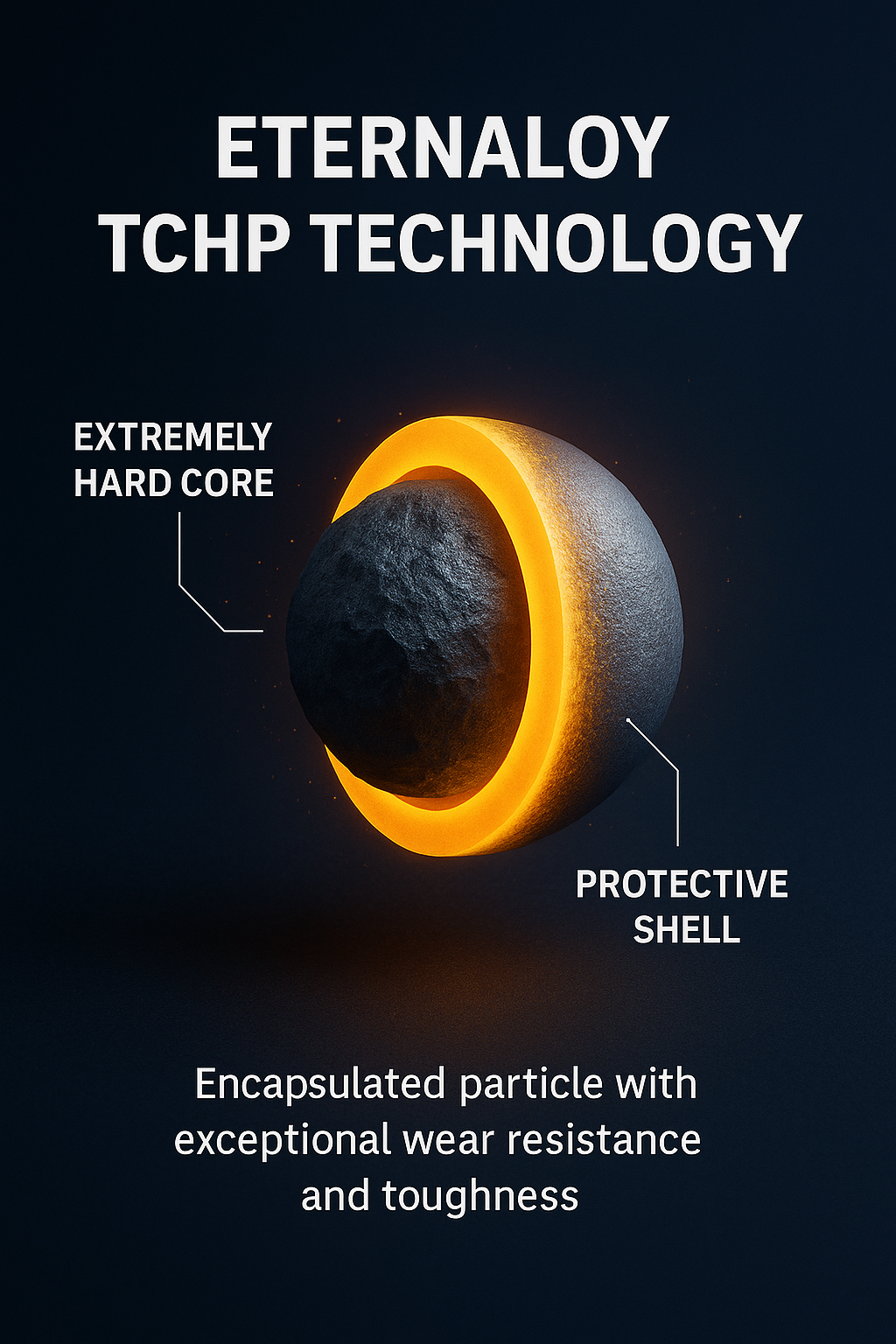
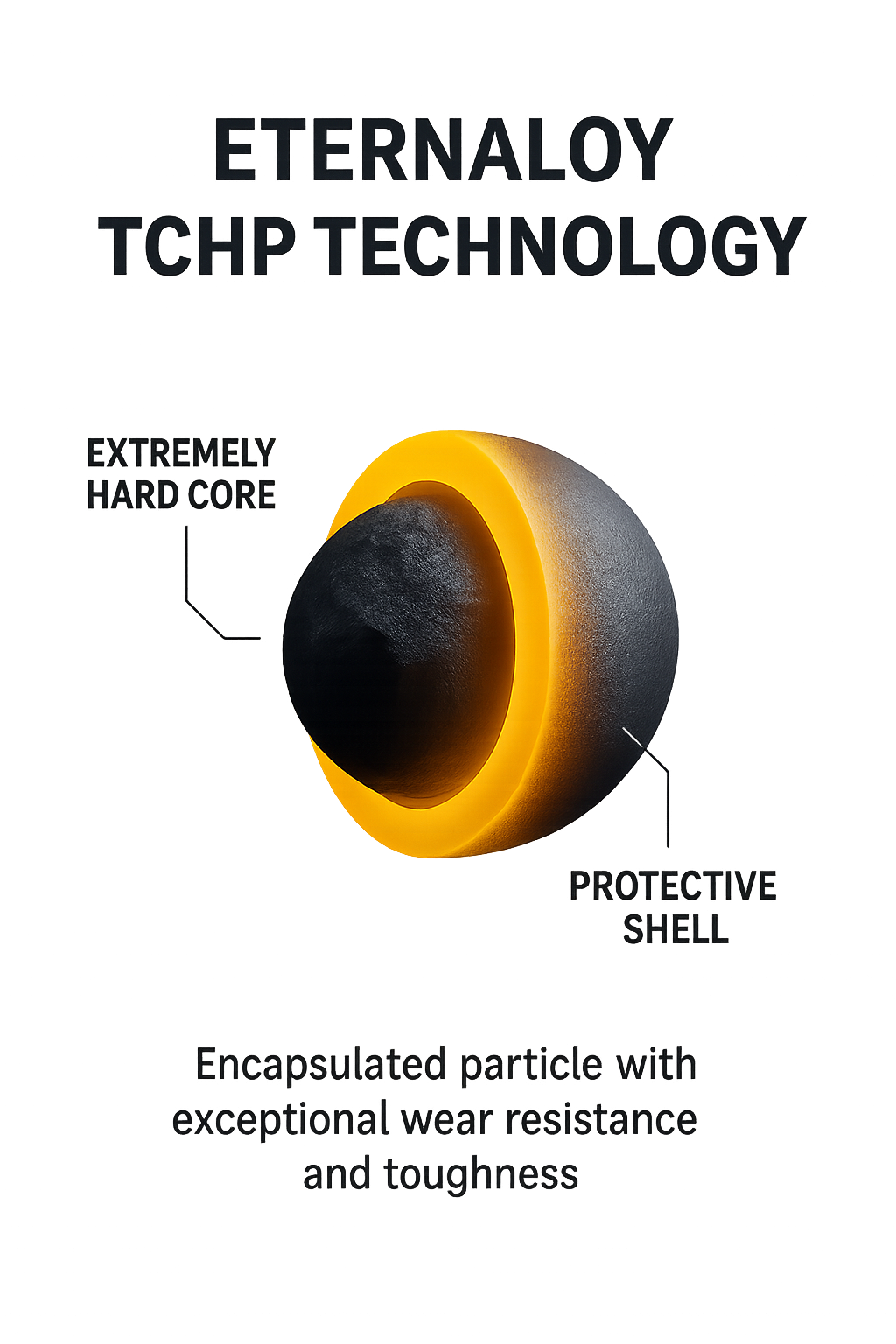
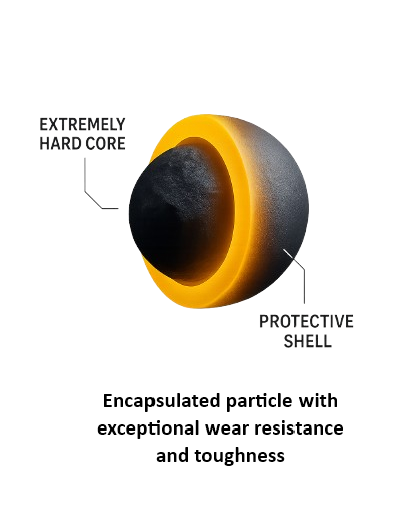
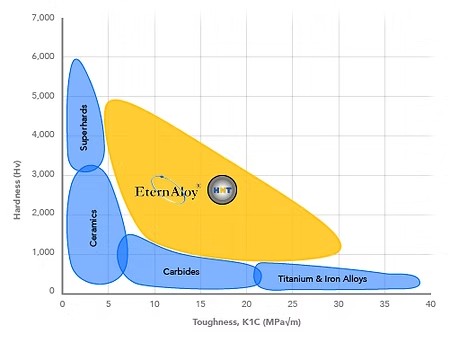
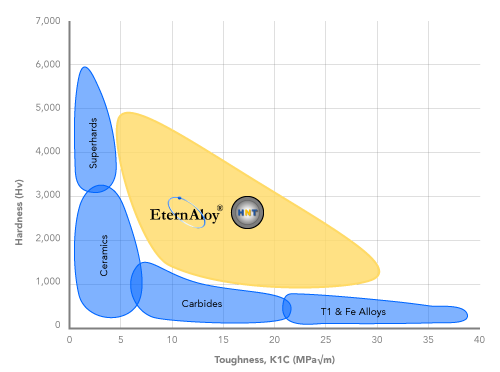
EternAloy Corporation’s surface coating powders are engineered for high-quality thermal spray applications, utilizing patented TCHP technology for superior wear resistance, corrosion protection, and surface enhancement in critical industrial components. These powders are trusted by manufacturers in aerospace, defense, energy, and manufacturing for their ability to deliver reliable performance in high-friction and high-temperature environments. Our surface coating powders extend the life of components, reduce maintenance costs, and improve operational efficiency.
Our product line includes a range of TCHP-based powders, each formulated for specific industrial needs. Whether you require powders for plasma spray, HVOF, or flame spray, EternAloy provides solutions that optimize surface hardness, reduce friction, and protect against corrosion. Our technical team offers expert support to help you select the right powder for your application and process.
Key features of our surface coating powders:
- Patented TCHP technology for enhanced surface properties
- High-performance powders for thermal spray and coating processes
- Consistent quality and reliable supply chain
- Technical support for process optimization and troubleshooting
Applications include turbine blades, engine components, wear parts, and precision tools. Our powders are trusted by leading manufacturers for their ability to improve surface hardness, reduce friction, and extend service life. Contact EternAloy for custom powder development, technical data sheets, and expert guidance on selecting the right powder for your application.
Available Surface Coating Powders
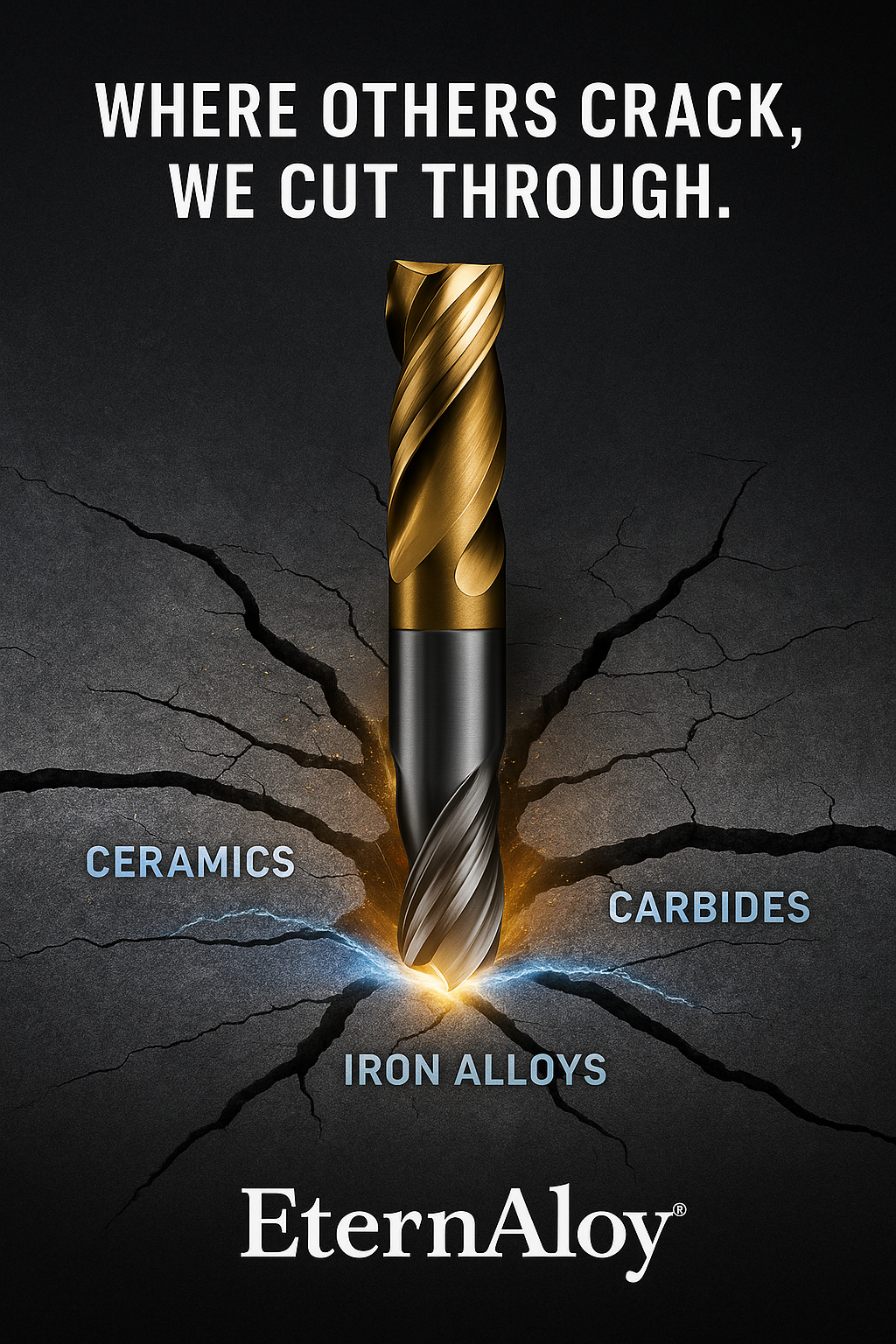
TCHP Surface Coating Powder
High-quality surface coating powder with TCHP for wear-resistant thermal spray, corrosion protection, and precision industrial coatings.
Request a Custom Quote
Tell us about your application and requirements. We'll respond with a tailored recommendation and pricing.