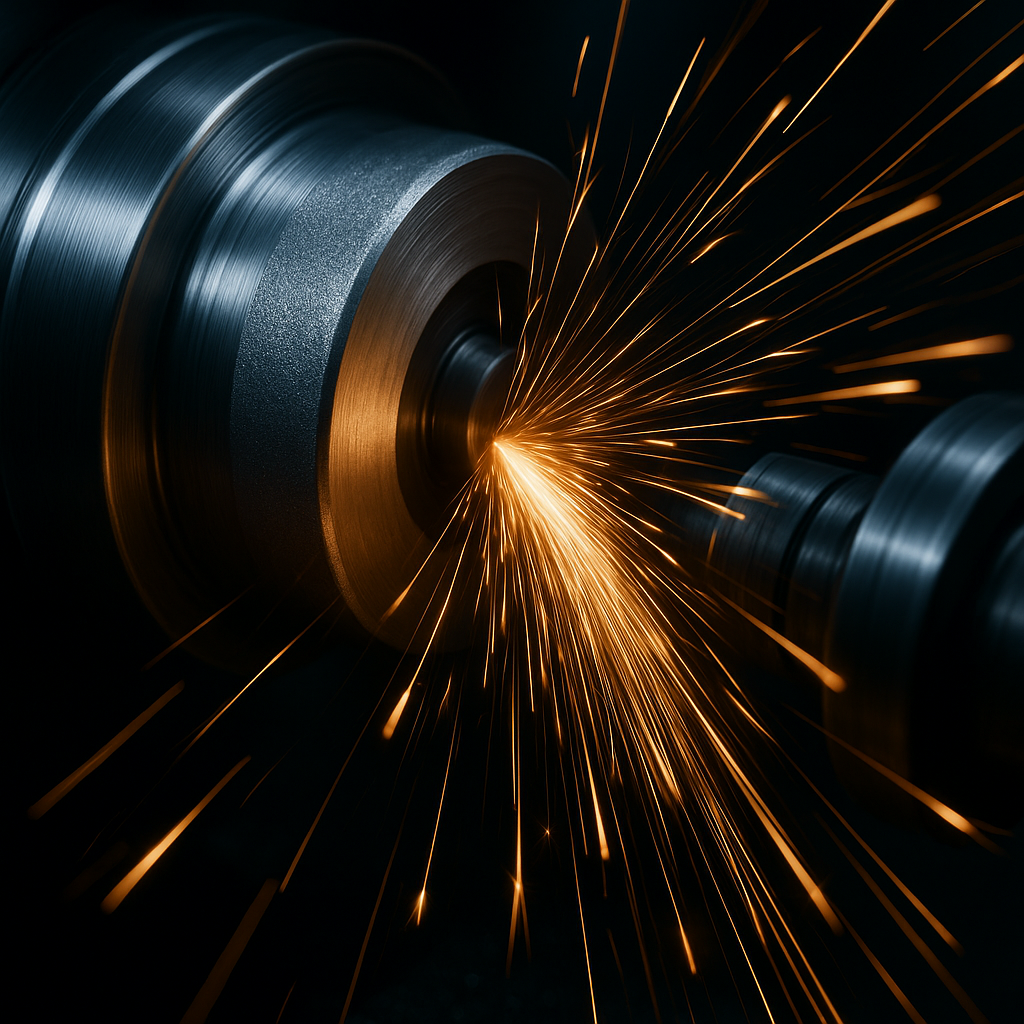
Our Mission
At EternAloy, our mission is to lead the world in delivering advanced, high-performance Tough-Coated Hard Powders across a broad range of industries. We are relentless in refining every aspect of our operation from quality assurance and technical precision to personalized service and on-time delivery, ensuring that our customers always receive unmatched value, reliability, and performance.
Our Vision
We envision a world where innovation and collaboration redefine industrial performance. EternAloy builds lasting partnerships grounded in trust, integrity, and mutual respect. By fostering a safe, inclusive, and team-oriented culture, we uphold the highest standards of ethics, environmental responsibility, and global stewardship.

Our Capabilities
Our in-house capabilities span every step of the production chain, from powder synthesis and coating to sintering and product finishing. We are equipped to handle both large-scale production and small-batch prototyping with the same level of precision and care.
Our Technology
At the heart of our product lineup is Tough-Coated Hard Powder (TCHP), our proprietary innovation that encapsulates micron-sized hard core particles with ultra-thin nanocoatings. This process creates materials that withstand extreme wear and mechanical stress, making them ideal for high-friction environments and critical applications. Whether sintered into dense components or applied as coatings, TCHP delivers consistent, industry-leading performance.
Our Facility
Located in North Huntingdon, PA, our 30,000 sq. ft. engineering and manufacturing facility is designed for innovation and scalability. The site includes advanced material processing labs, high-temperature furnaces, coating systems, and quality assurance infrastructure, all under one roof. This vertical integration enables us to accelerate product development, ensure quality at every stage, and adapt quickly to customer needs.
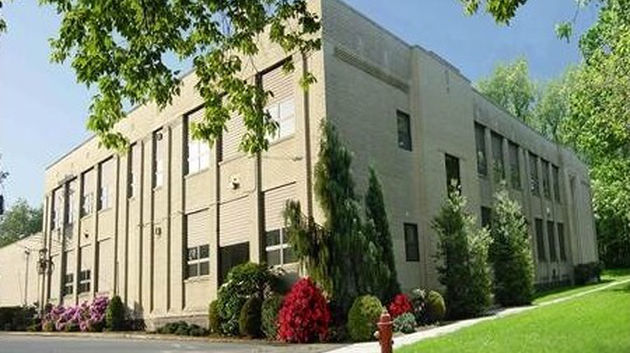
Meet Our Team
Get to know the experts behind our innovative materials and exceptional service.
Meet the TeamExplore Our Products
Discover our complete range of advanced materials and cutting tools.
Browse Products